-
100% sustainable
-
+50 years of experience
-
50% stackable
-
800 clients
Expert in plastic projects
From design to production, we have been helping our customers for over 50 years by creating plastic products, stackable crates and custom moulding. Our guarantee is to offer top quality and service to our clients.
What can we do for you?
Custom moulding
Custom moulding allows us to create the plastic parts needed within the packaging industry, logistics sector, construction and electronics. Thanks to our versatile and highly automated machine park, we can produce everything from very small objects to larger plastic components with precision and quality.
Standard crates
Our standard crates are produced according to Euro standards for modular packaging and transport and approved for food. Available with open or perforated bottom and always perfectly traceable.
Custom crates
At your request, we also design completely new containers when the numbers or the project allow for a new mould investment.
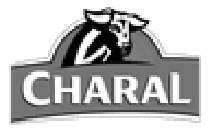
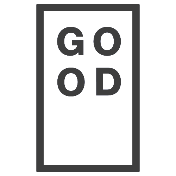
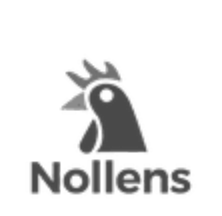
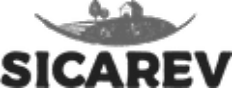
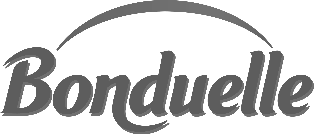
A crate for every sector
We offer solutions for various industries, including the meat and poultry industry, bakery industry and fishing industry. Our crates meet Euro standards for maximum pallet and truck compatibility, and are made from food-grade raw materials.
Meat and poultry sector
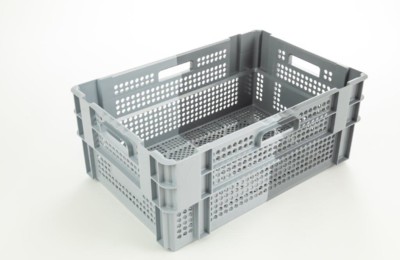
- Reduced volume
- Strong & practical
- Easy to clean
Bakery sector

- Reduced volume
- Strong & practical
- Easy to clean
Fishing sector
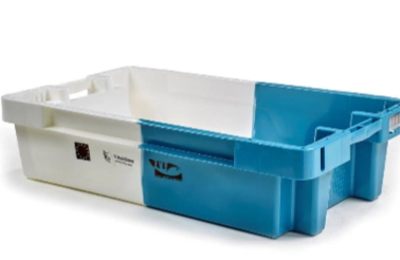
- Reduced volume
- Strong & practical
- Easy to clean
Do you need plastic crates to be used in another industry? We can help you as well. Please feel free to contact us for further assistance.
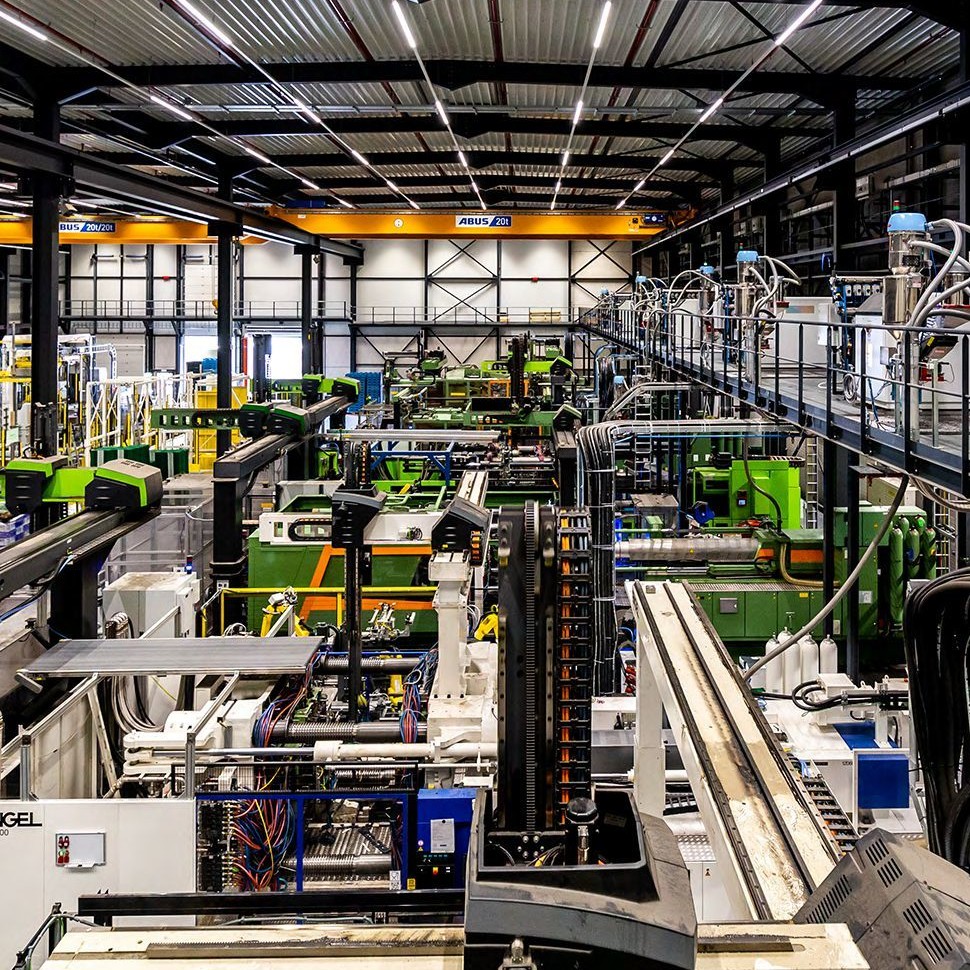
High-tech machinery
Our versatile and highly automated machine park consists of more than 40 injection moulding machines, with a clamping force ranging from 25 to 3000 tons. These machines produce 24 hours a day, 7 days a week. With this machine park, we can manufacture plastic products > 10 kg and surfaces up to 2m². Our processes are fully automated and customer-specific. Engineering is carried out entirely in-house.
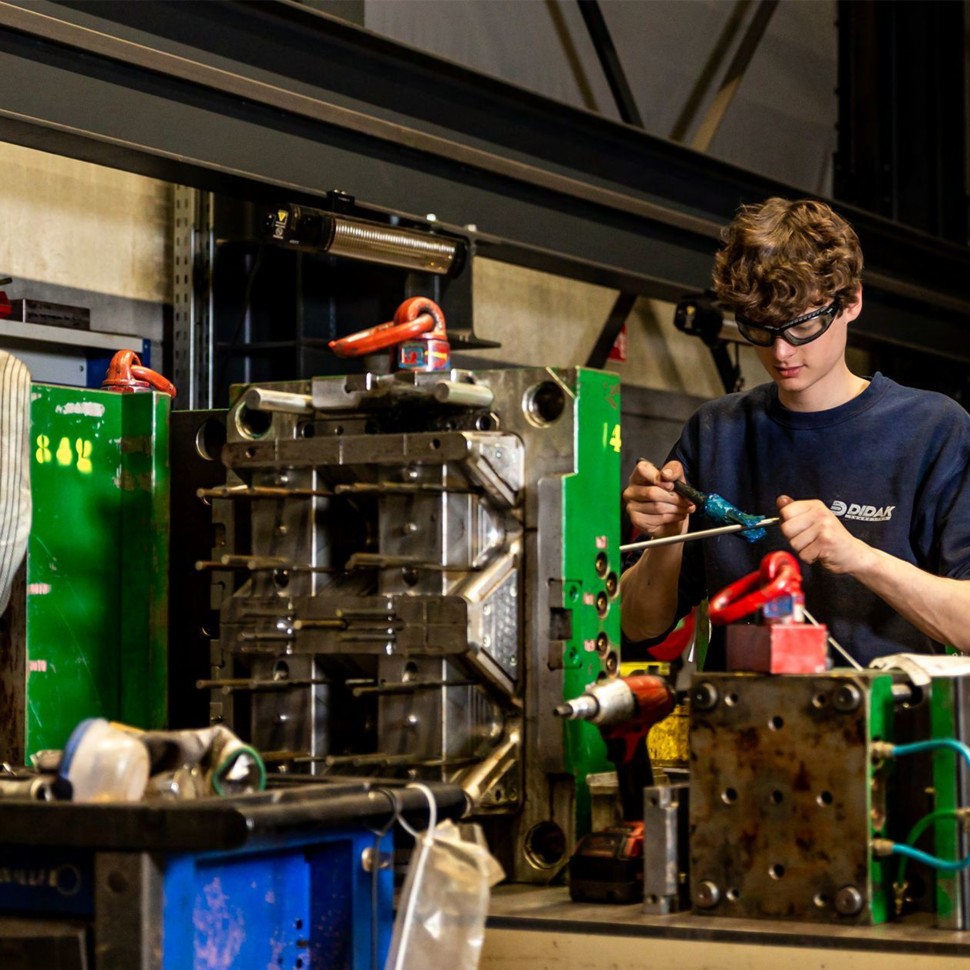
Mould and mould maintenance
High-quality and accurate moulds are essential for the production of high-quality plastic products. At Didak Injection we have our own mould department, where moulds are designed and maintained. Our mould technicians are trained for the revision and repair of moulds and are ready to intervene when interventions or optimisations are required.
Since we have an in-house mould department, delays and stoppages (which represent additional costs) in the production process are kept to a minimum.