Transformation at multiple levels
The redesign of the flower crate brought several improvements, all aimed at optimising the logistics process. The old crate was too heavy and not flexible. As a result, it could only be fully stacked with the help of a metal handle, which generated a lot of noise in the production area. At Didak Injection, we injection-molded the new flower crate, as well as the new handle, which is now made of plastic. This offers a great advantage for recycling, as the crate is now made from a single material (monomaterial).
As initiators, Heemskerk Flowers Rijnsburg, Van der Plas Rijnsburg (Floral Trade Group), Celdomy Honselerdijk, and Argos Packaging Honselerdijk have found an ideal partner in Didak to bring their development into production.
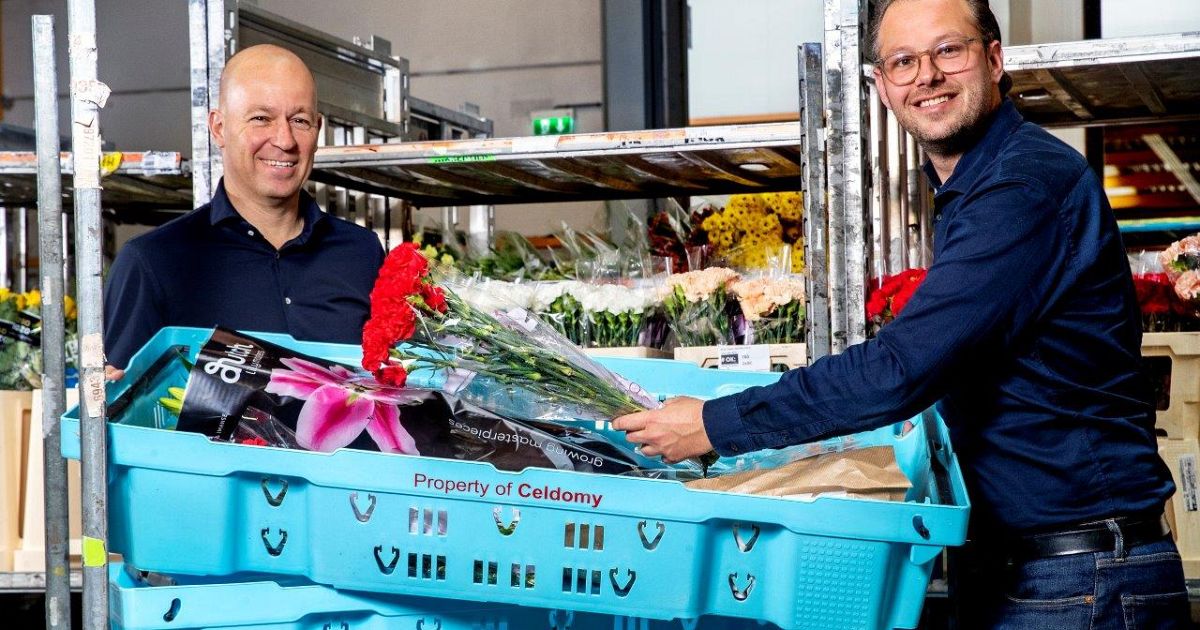
In this new version, the metal handle has been replaced with a plastic version, improving recyclability. The crates can now be stacked up to 60%, allowing for economical transport at 50% load capacity. Additionally, the handle can now fold into the rim of the crate, so it no longer obstructs when the crates are nested empty.
To prevent deformation, the crate has been made sturdier, and we increased the capacity from 112 liters to 122 liters. By modifying the U-shaped edge into a straight edge and using plastic with a foaming agent, we reduced the height while maintaining strength. The result: a solid business case, as truck loads (and therefore costs) remained equivalent to those of cardboard boxes, while benefiting from the advantages of a sustainable crate.
A third optimisation involved adding leaf-shaped notches on the sides of the crate, allowing rubber bands to be easily attached to hold the flowers in place during transport. Cutouts were made on the upper rim for PP plastic straps. A printed cardboard sheet is placed over the flowers and securely fastened with 1 to 3 plastic straps.
Additionally, we designed the labeling areas with embossing to make stickers easier to remove and integrated RFID tags into the wider top rim for better automation. The bottom of the crate is equipped with a rim and a ribbed pattern for better grip on conveyor belts – an important improvement for automated processes.