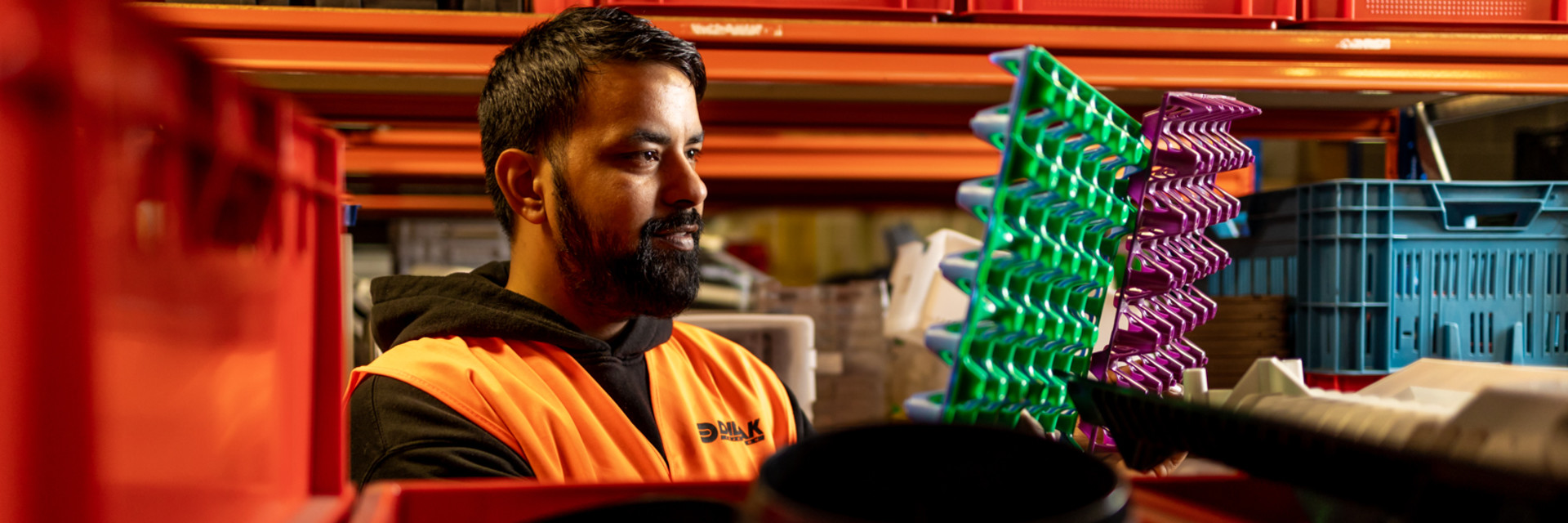
From idea to finished (end) product in 6 steps
Custom moulding allows you to go in many directions. In a flexible and cost-efficient manner, we can produce a wide range of durable products in large quantities.
Do you already have a design, or are you starting from scratch? At any stage, we can bring your project to successful completion.
Here’s how Didak Injection turns your ideas into reality:
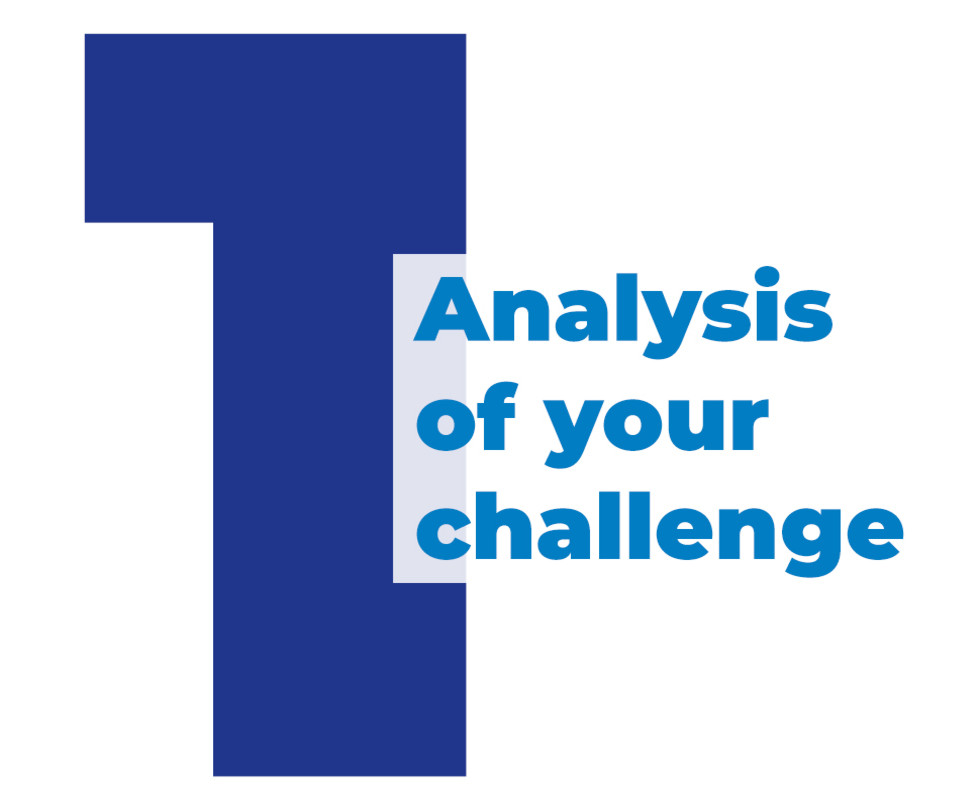
Every project starts with an in-depth analysis of your needs and objectives. Whether it is finding a specific product or component, developing an innovative concept, or improving an existing product, our experienced engineers are ready to ask the right questions and provide solutions.
And it doesn’t have to start from scratch. Re-engineering is also possible: rethinking an existing product to improve it or adapt it to new requirements. For example, a metal part can be replaced by a plastic part to become lighter, more efficient, or more durable.
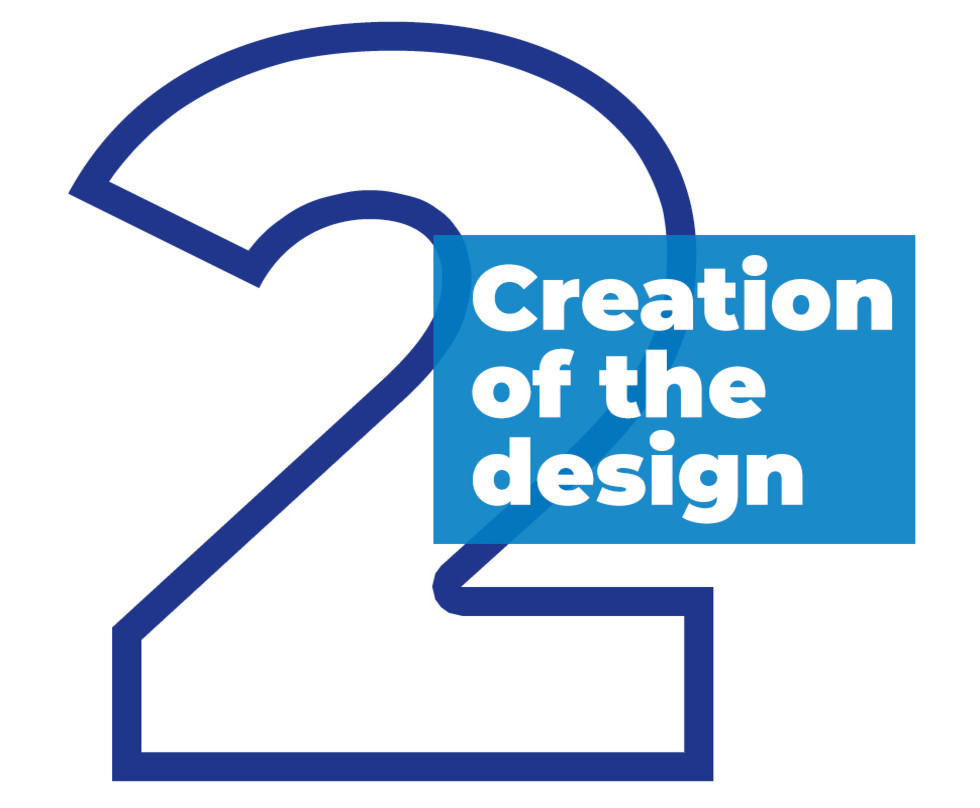
Our team of experts combines technical knowledge with creative flair to create a design that meets your expectations in terms of both functionality and aesthetics. Because we strive for perfection in every detail, your input is crucial in this design.
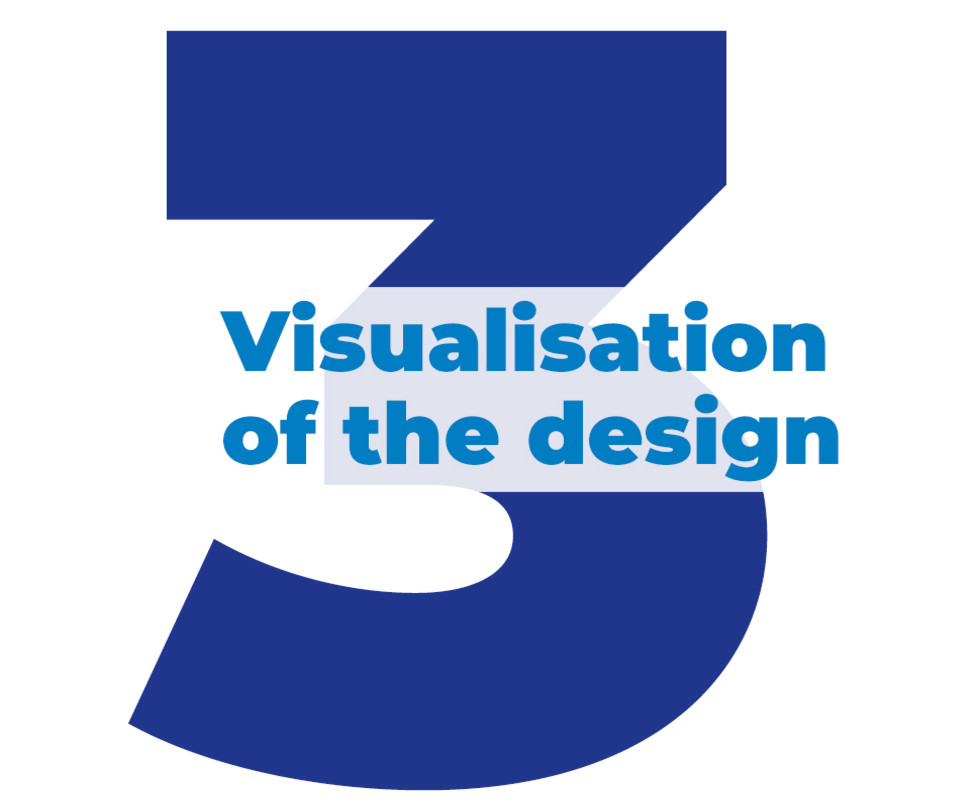
Based on a validated design proposal, we create a detailed drawing and 3D model. This allows us to view the design from all angles and identify any issues before production begins.
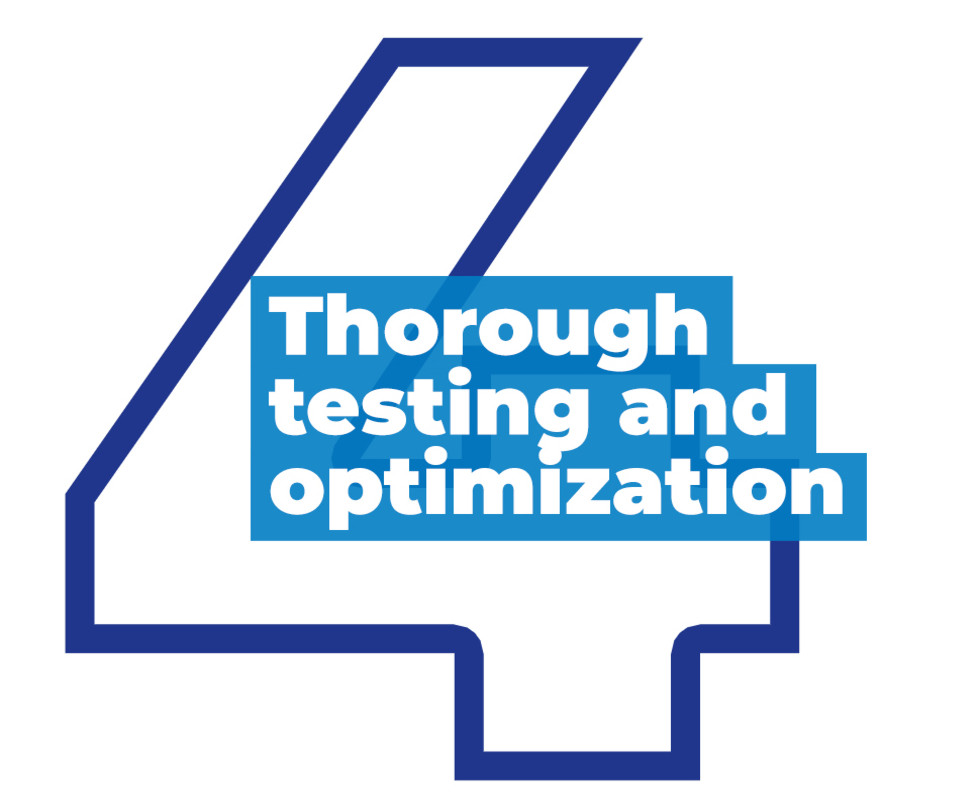
Is the design approved? We conduct extensive tests to ensure that the final product meets the highest standards and expectations. We test all possible aspects, ranging from functionality, dimensions, weight, load capacity, wall thickness, density, etc.
Due to the cooling and hardening of the material, shrinkage can occur. We also test this thoroughly to ensure that the product retains its functionality. In addition, we check whether the colour remains consistent across all produced parts.
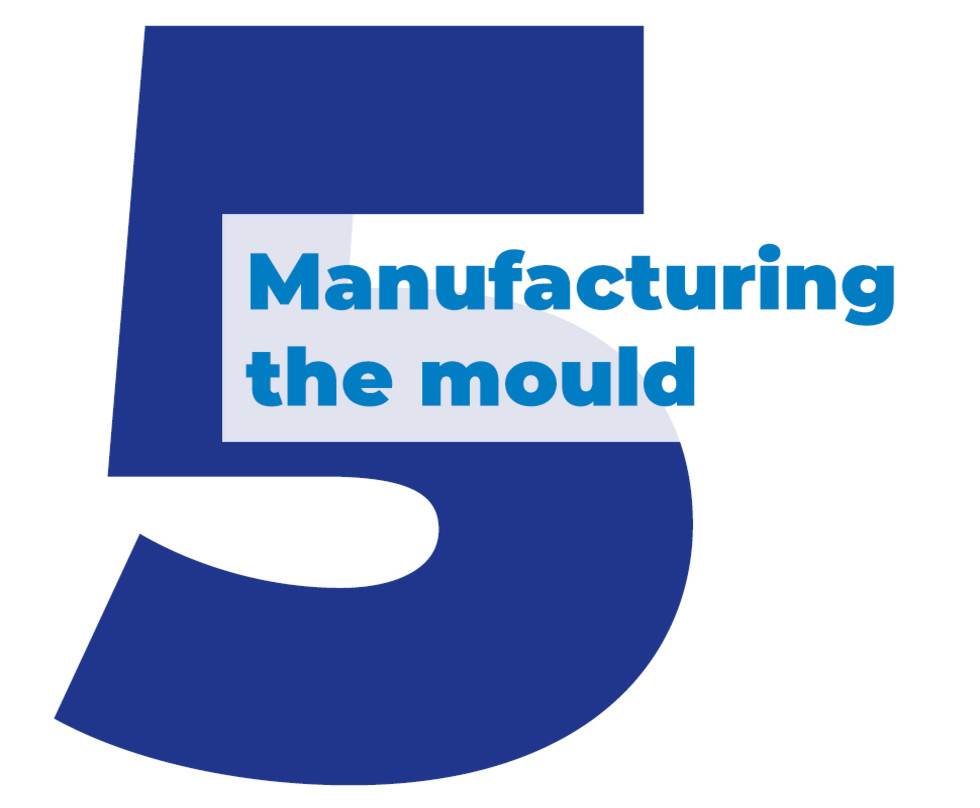
Once the design is completed and thoroughly tested, we can start making the mould, a precision tool used to inject molten plastic into the desired shape. Our expertise and years of experience ensure a smooth process and accurate and consistent end result.
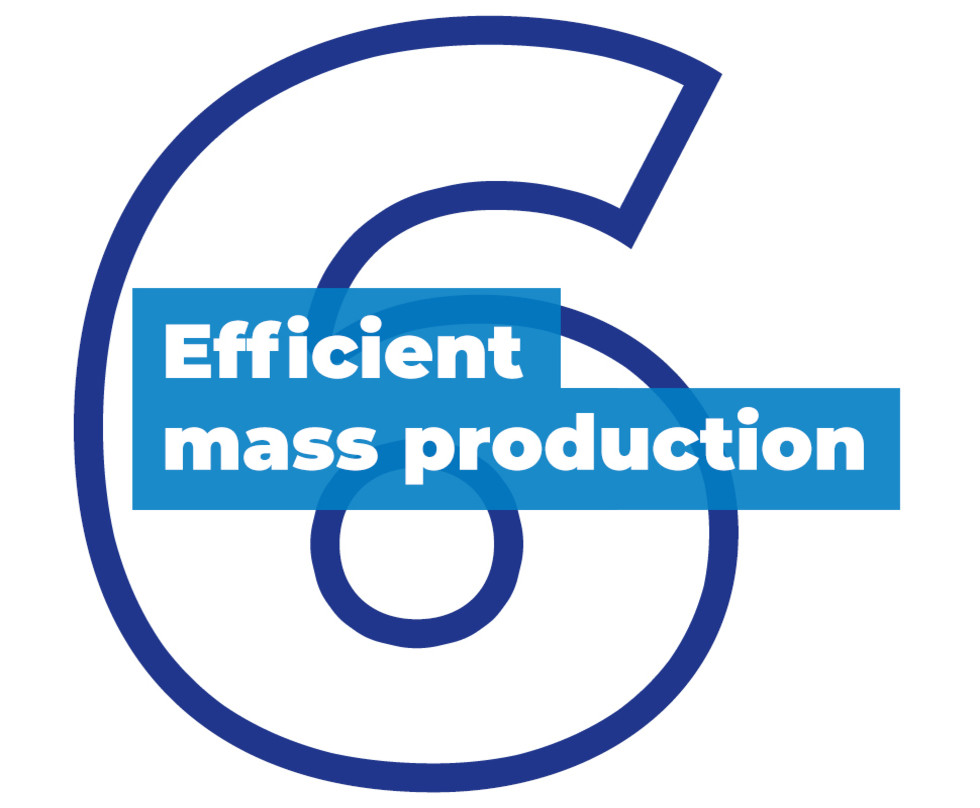
With the mould in place, we can move on to production. Thanks to advanced automation, we can quickly and cost-effectively produce large quantities. The packaging and loading of trucks are also done automatically and efficiently.
Once a production run is completed, we store and maintain your mould for reuse, keeping production cost-efficient in the long term.